Amin, A. K. M. Nurul and Ginta, Turnad Lenggo and Ishtiyaq, M. H.
(2011)
Modeling for surface roughness in end-milling of Titanium alloy Ti-6Al-4V using uncoated WC-Co inserts.
In:
Advanced Machining Towards Improved Machinability of Difficult-to-Cut Materials.
IIUM Press, Kuala Lumpur, Malaysia, pp. 161-166.
ISBN 9789674181758
![[img]](http://irep.iium.edu.my/style/images/fileicons/application_pdf.png) 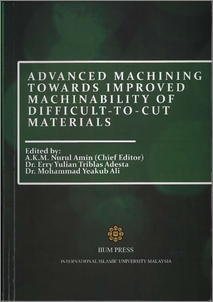 Preview |
|
PDF ( Modeling for surface roughness in end milling of Titanium alloy Ti-6Al-4V using uncoated WC-Co inserts )
- Published Version
Download (565kB)
| Preview
|
Abstract
Titanium alloys are widely known as difficult to cut materials, especially at higher cutting
speeds, due to their several inherent properties. Among all titanium alloys, Ti-6Al-4V is most
widely used, so it has been chosen as the workpiece material in this study. Siekmann [1]
suggested that machining of titanium and its alloys would always be a problem, no matter
what techniques are employed to transform this metal into chips. When machining Ti-6Al-
4V, conventional tools wear rapidly because the poor thermal conductivity of titanium alloys
resulting in higher cutting temperature closer to the cutting edge. There also exists strong
adhesion between the tool and workpiece material [2]. Since the performance of conventional
tools is poor in machining Ti-6Al-4V, a number of newly evolved tool materials, such as
cubic boron nitride (CBN) and polycrystalline diamond (PCD), are being considered to
achieve high-speed milling [3].
In order to establish an adequate functional relationship between the responses (such as
surface roughness, cutting force, tool life/wear) and the cutting parameters (cutting speed,
feed, and depth of cut), a large number of tests are needed for each and every combination of
cutting tool and work piece materials. This increases the total number of tests and as a result
the experimentation cost also increases. Response Surface Methodology (RSM), as a group of
mathematical and statistical techniques, is useful for modeling the relationship between the
input parameters (cutting conditions) and the output variables. RSM saves cost and time by
reducing the number of experiments required. A machinability model may be defined as a
functional relationship between the input of independent cutting variables (speed, feed, depth
of cut) and the output known as responses (tool life, surface roughness, cutting force, etc) of a
machining process [4].
Response surface methodology (RSM) is a combination of experimental and regression
analysis and statistical inference. RSM is a dynamic and foremost important tool of design of
experiment (DOE), wherein the relationship between response(s) of a process with its input
decision variables is mapped to achieve the objective of maximization or minimization of the
response properties [5-6]. Many machining researchers have used response surface
methodology to design their experiments and assess results. Kaye et al [7] used response
surface methodology in predicting tool flank wear using spindle speed change. A unique
model has been developed which predicts tool flank wear, based on the spindle speed change,provided the initial flank wear at the beginning of the normal cutting stage is known. An
empirical equation has also been derived for calculating the initial flank wear, given the
speed, feed rate, depth of cut and workpiece hardness. Alauddin et al [8] applied response
surface methodology to optimize the surface finish in end milling of Inconel 718 under dry
condition. They developed contours to select a combination of cutting speed, and feed
without increasing the surface roughness.
In this paper, the RSM technique is used in developing a mathematical model to optimize the
surface roughness values when end milling titanium alloy using both uncoated WC-Co inserts
under dry conditions. Factorial design coupled with response surface methodology is utilized
to develop the model for predicting surface roughness values.
Actions (login required)
 |
View Item |