Amin, A. K. M. Nurul and Hafiz, A.M. Khalid and Lajis, M. A.
(2011)
Modeling of surface roughness during end milling of AISI H13 hardened tool steel.
In:
Advanced Machining Towards Improved Machinability of Difficult-to-Cut Materials.
IIUM Press, Kuala Lumpur, Malaysia, pp. 167-173.
ISBN 9789674181758
![[img]](http://irep.iium.edu.my/style/images/fileicons/application_pdf.png) 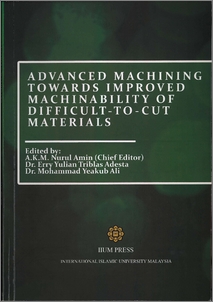 Preview |
|
PDF (Modeling of surface roughness during end milling of AISI H13 hardened tool steel)
- Published Version
Download (564kB)
| Preview
|
Abstract
Hard machining, a frequently used term in today’s machine tool industries, refers to the
machining of material with a hardness value over 45 HRC. The concept of hard machining was
developed in 80s; however, the prevalent industrial implementation of hard part machining was
adopted during the last decade [1]. Advantages in hard machining incorporate the complete
machining process with a single fixture setup, eliminating intermediate heat treatment and final
grinding process while still meeting the dimensional and surface roughness specifications [2].
The widespread demand of hardened tool steel like AISI H13 requires high speed machining
(HSM). Over the last decade, HSM has been used to manufacture molds/dies made from AISI
H13. Many progressive works have been carried out to improve the high speed machining
performance of H13. However, despite the significant importance of surface finish most of the
machining researchers to date have concentrated on chip morphology, tool life and wear
mechanism. In hard part machining, surface finish is a major quality criterion. With an accurate
level of roughness it is possible to eliminate final grinding process, sometime even the hand
polishing [3]. Considering its importance some researchers conducted their studies on surface
quality during hard machining. Choudhury at el. [4] applied Taguchi method for the prediction of
surface roughness during the end milling of AISI H13 tool steel and found that roughness value
tends to decrease with increasing cutting speed and decreasing feed rate. El-Baradie [5] drew
similar conclusion on cutting speed. He observed that increase of cutting speed maximizes
productivity, at the same time, it improves surface quality. However, in all of the above cases
and other works related to the surface roughness study it was found that the lowest achievable
surface finish was only 0.2 μm. at high cutting speed mode. In most of the cases roughness
values were sufficiently high to fall in the grinding region (above 0.2 to 0.4 μm). Moreover,
material removal rate was limited for using lower radial depth of cut and feed per tooth (Rd = 0.3
mm to 0.8 mm and f = 0.10 mm/tooth).
In this context, considering the influence of surface finish on mold/die for net shape
manufacturing, current paper deals with the performance of PCBN and PVD-TiAlN coated carbide tool inserts in terms of surface roughness during the end milling of H13 hardened tool
steel (52 HRC). In this regard, mathematical models based on the experimental results were
developed in order to predict the surface finish during the end milling of H13 hardened tool steel.
Actions (login required)
 |
View Item |