Amin, A. K. M. Nurul and Abdelgadir, M. and Kamaruddin, K.
(2011)
Some aspects of improved machinability in preheated machining of Titanium alloy Ti-6Al-4V.
In:
Advanced Machining Towards Improved Machinability of Difficult-to-Cut Materials.
IIUM Press, Kuala Lumpur, Malaysia, pp. 19-26.
ISBN 978-967-418-175-8
![[img]](http://irep.iium.edu.my/style/images/fileicons/application_pdf.png) 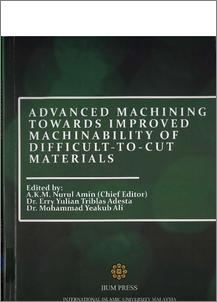 Preview |
|
PDF ( Some aspects of improved machinability in preheated machining of Titanium alloy Ti-6Al-4V)
- Published Version
Download (479kB)
| Preview
|
Abstract
Titanium and its alloys have found wide application in the aerospace, biomedical and
automotive industries owing to their good strength-to-weight ratio and high corrosion
resistance. However, these alloys have very poor machinability, which is attributed to their
inherent high strength maintained at elevated temperature and low thermal conductivity. High
chemical reactivity of titanium at high elevated temperatures, especially with titanium based
tools or coatings limit their application during machining. The strategy of titanium machining
is to use tools which show less reactivity, has higher thermal conductivity to increase the
chip-tool contact length and effectively take away the generated heat and to use tougher and
harder tools which could withstand the dynamic action of the cutting force. The
recommended tools for many years had been the uncoated tungsten carbide grade K.
However, modern trend is to use Poly Crystalline Diamond (PCD) tools for machining of this
particular alloy. In this work the effectiveness of PCD has been compared to that of uncoated
tungsten carbide tool in machining titanium alloy Ti-6Al-4V. The comparison has been made
in terms of the applicable cutting speed ranges, tool wear rates, tool wear morphology, chip
segmentation and chip-tool contact lengths.
Titanium and its alloys have been experiencing extensive development over the past few
decades stimulated by a series of their unique properties, such as, high strength to weight
ratio maintained at elevated temperatures, high fracture resistance and exceptional resistance
to corrosion at temperatures below 500 0C. Though the initial applications of Titanium alloys
have been in the aerospace industries in aero-engine and airframe manufacture, there is a
growing trend in their application in the industrial sector, which includes petroleum refining,
chemical and food processing, surgical implantation, nuclear waste storage, automotive and
marine applications. Despite the increased usage and production of titanium and its alloys,
these materials fall under the category of the most difficult to machine materials which is
attributed to their inherent high strength property maintained at elevated temperature and also
their tendency to form localized shear bands during machining [1, 2]. Apart from that the
thermal conductivity of Ti–6Al–4V alloy (7 Wm−1 K−1) is very low (86% lower) compared
to that of AISI 1045 steel (50 Wm−1 K−1) [1]. The heat affected zone is also very small as a result of the shorter chip-tool contact length (about 1/3 that of the contact length for steel) [1,
3, 5]. As a result high cutting temperatures are generated during machining of titanium alloys
and the hottest point is brought close to the cutting edge. The temperature zone of 700 0C
comes as close as 0.1 mm from the cutting edge. On the other hand, the stresses acting on the
tool are dynamic in nature due to the formation of chips with serrated teeth in the entire cutting
speed range [4-5]. The other reason for poor performance of the tool is the chemical
reactivity of titanium [6-8]. Attempts to describe the chip morphology in cutting titanium and
its alloys date back to the work performed by Cook in 1953 [9]. Straight tungsten carbide
(WC/Co) tools are reported to have superiority in performance in machining Ti alloys in
interrupted cutting [10,11]. Shuting and Wenjieapplied High-Speed Machining of Titanium
Alloys using the Driven Rotary Tool and found reported high tool life [12]. Modern trend of
machining is using PCD or Poly Crystalline Cubic Boron Nitride (PCBN) tools [2].
It may be concluded from these works that uncoated cemented carbide and the PCD are the
most suitable cutting tool materials for titanium machining. Comparison of the performance
of these two materials and the basic mechanism of their improved performance from the
perspective of chip formation instability, contact length and the tool strength in withstanding
mechanical failure and chemical action needs to be performed.
Actions (login required)
 |
View Item |