Amin, A. K. M. Nurul and Ginta, Turnad Lenggo
(2011)
Machinability improvement in end milling of Titanium Alloy Ti-6Al-4V through preheating.
In:
Advanced Machining Towards Improved Machinability of Difficult-to-Cut Materials.
IIUM Press, Kuala Lumpur, Malaysia, 09-17.
ISBN 978-967-418-175-8
![[img]](http://irep.iium.edu.my/style/images/fileicons/application_pdf.png) 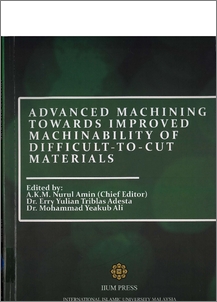 Preview |
|
PDF (Machinability improvement in end milling of Titanium Alloy Ti-6Al-4V through preheating )
- Published Version
Download (481kB)
| Preview
|
Abstract
Titanium alloys are used widely in the aerospace, chemical and ship building industry because of
their superior mechanical properties, heat resistance and corrosion resistance. Titanium alloys,
however, are materials that are extremely difficult to machine. During the machining of titanium
alloy, tool wear progresses rapidly because of the high cutting temperature and strong adhesion
between the tool and the work material, owing to their low thermal conductivity and high
chemical reactivity [1,2]. However, by properly selecting the tool material and cutting conditions
an acceptable rate of tool wear may be achieved and thus lowering the total machining cost [3].
The performance of a cutting tool is normally assessed in terms of its life. Mostly, flank wear is
considered, since it largely affects the stability of the cutting wedge and consequently the
dimensional tolerance of the machined work surface [4].
The use of workpiece preheating (hot machining) as a technique for improving machining
operations has been under consideration since the late 19th century. This was informed by
understanding that metals tend to deform more easily when heated, thus enhancing machining.
The principle behind hot machining is increasing difference in hardness of the cutting tool and
workpiece, leading to reduction in the component forces, improved surface finish and longer tool
life [5]. Amin and Talantov [6] studied the influence of the furnace method of preheating of
workpiece on machinability of titanium alloy BT6 (Russian Standard) and found that the vertical
cutting force component decreases with the increase in the preheating temperature but the radial
and the axial components sharply increase to their peak values at a particular temperature. Ozler
et al [7] used gas flame heating to improve the machinability of austenitic manganese steel.
Wang et al [8] performed LAM using YAG continuous solid laser on Al2O3 particle reinforced
aluminum matrix composite (Al2O3p/Al). The result of their study showed that in machining of
Al2O3p/Al composite the cutting force was reduced by 30-50 %, tool wear was reduced by 20-30
% in laser assisted machining as compared with conventional cutting. Tosun and Ozler [9]studied hot machining in turning high manganese steels using liquid petroleum gas flame under
different cutting conditions of feed rate, depth of cut, cutting speed and surface temperature and
developed a mathematical model for tool life from the experimental data using a regression
analysis method.
The main objective of this study is to investigate the effect of workpiece preheating with high
frequency induction heating on improvement of tool life of uncoated WC-Co inserts during end
milling of titanium alloy Ti-6Al-4V. Tool wear, vibration, and cutting force were investigated
during the experiments.
Actions (login required)
 |
View Item |