Hossain, Ishtiaq and Amin, A. K. M. Nurul and Patwari, Muhammed Anayet Ullah and Ginta, Turnad Lenggo
(2011)
Assessment of performance of uncoated and coated carbide inserts in end milling of Ti-6Al-4V through modelling.
In:
Advanced Machining Towards Improved Machinability of Difficult-to-Cut Materials.
IIUM Press, International Islamic University Malaysia, Kuala Lumpur, Malaysia, pp. 195-202.
ISBN 9789674181758
![[img]](http://irep.iium.edu.my/style/images/fileicons/application_pdf.png) 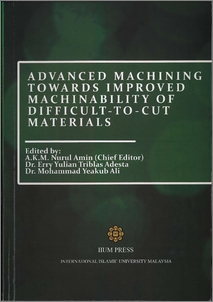 Preview |
|
PDF ( Assessment of performance of uncoated and coated carbide inserts in end milling of Ti-6Al-4V through modelling)
- Published Version
Download (564kB)
| Preview
|
Abstract
Materials used in the manufacturing of aero-engine components generally comprise nickel
and titanium base alloys. A major requirement of cutting tool materials used for machining
aero-engine alloys is that they must possess adequate hot hardness to withstand the elevated
temperatures generated at high speed conditions of aerospace alloys. Most cutting tool
materials lose their hardness at elevated temperatures resulting in the weakening of the interparticle
bond strength and consequent acceleration of tool wear which results in deterioration
of surface roughness. So it is very essential to establish an adequate functional relationship
between the responses (such as surface roughness, tool life) and the cutting parameters
(cutting speed, feed and depth of cut). Response surface methodology (RSM) may help in
establishing the relationships between surface roughness and the cutting parameters for
coated and uncoated inserts. The method was introduced by G.E.P Box and Wilson [1]. The
main idea of RSM is to use a set of designed experiments to obtain an optimal response with
limited number of experiments to save cost and time. RSM is a dynamic and foremost
important tool of design of experiment (DOE), wherein the relationship between response(s)
of a process with its input decision variables is mapped to achieve the objective of
maximization or minimization of the response properties [1,2]. Many machining researchers
have used response surface methodology to design their experiments and assess results.
Analytical models have been created to predict surface roughness and tool life in terms of
cutting speed, feed and axial depth of cut in milling steel material [3] and [4]. An effective
approach has also been presented to optimize surface finish in milling Inconel 718 [5]. Kaye
et al [6] used response surface methodology in predicting tool flank wear using spindle speed
change. Wu [7] first pioneered the use of response surface methodology in tool life testing.
Thomas et al. [8] used a full factorial design involving six factors to investigate the effects of
cutting and tool parameters on the resulting surface roughness and on built-up edge
formatting in the dry turning of carbon steel. Choudhury and El-Baradie [9] had used RSM
and 23 factorial designs for predicting surface roughness when turning high-strength steel.
The main objective of the current work was to develop RSM models for surface roughness
based on cutting speed, axial depth of cut and feed for uncoated and coated inserts and then
coupling GA with the developed RSM model to optimize the cutting conditions to search out
the minimum surface roughness.
Actions (login required)
 |
View Item |