Amin, A. K. M. Nurul and Zakaria, Ahmad Farhan and -, Syadatul Akma
(2011)
Application of permanent electromagnet for chatter control in end milling of Titanium alloy - Ti6Al4V.
In:
Advanced Machining Towards Improved Machinability of Difficult-to-Cut Materials.
IIUM Press, Kuala Lumpur, Malaysia, pp. 99-106.
ISBN 9789674181758
![[img]](http://irep.iium.edu.my/style/images/fileicons/application_pdf.png) 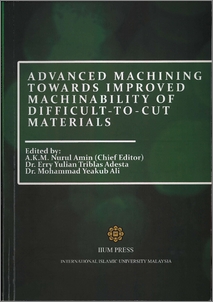 Preview |
|
PDF ( Application of permanent electromagnet for chatter control in end milling of Titanium alloy - Ti6Al4V)
- Published Version
Download (568kB)
| Preview
|
Abstract
Chatter is a vibration that occurs during machining operations resulting from instability of the
cutting process with system responses of the spindle tool chuck system. One of the most
challenging issues in machining process is to know the chatter characteristics. The main problem
with chatter is that its mechanics is still not yet fully understood. Chatter is inconsistent in
character, making it difficult to analyze and predict. This research work investigates the
performance of permanent magnet in suppressing the chatter phenomena in end milling
operation. An experiment is designed based on response surface methodology (RSM)
approach using DESIGN EXPERT software. The experiments are done under two different
conditions. The first condition is without the presence of magnet while the other is with
the presence of magnet. Titanium alloy (ti-6al-4v) WAS used as a work material. Chatter
or vibration with high amplitude appears in the system during end milling at cutting speed 70
m/min when the frequency of chip formation instability, associated with the formation of serrate
chip. Cutting under the existence of magnet did suppress the chatter about 40% and the surface
roughness is much better and smoother with the magnet compared to the cutting under room
temperature in general.Machining of metal is usually accompanied by a violent relative vibration
between work and tool, known as chatter. Chatter arises as a result of resonance caused by the
interaction of the vibrations due to the instability of chip formation and natural vibrations of the
system components. Campa et al. [1] described chatter as a dynamic problem at high removal
rate condition. In addition Quintana et al. [2] specified that chatter can be obviously predicted
from the loud noise and the poor surface integrity due to the chatter mark. In machining process,
there are some problems that propagate the end of result especially in metal cutting. Y. Altintas
and Philips K. Chan [3] stated that one of the major limitations on productivity in metal cutting is
chatter vibration, which cause poor surface finish and tool damage. Kim et al. [4] explained that
most of the drawbacks comes from chatter is causes excessive tool wear, noise, tool breakage,
and deterioration of the surface quality. According to Patwari et al. [5] chatter is a very important
phenomenon that needs to be taken into consideration whenever machining process is being
performed. Amin et al. [6] and Patwari et al. [7] found that the root cause of chatter lies in the
coincidence of the frequency of instability of chip formation with one of the natural frequencies
of the machine-spindle-tool system components during end milling machining operation There have been several attempts in increasing the stability limit in cutting. Opitz and
Bemardi [8] developed a general closed lobes representation of dynamic machining
operation that can be applied to both turning and milling. Stone [9] extended the nonuniform
pitch concept by proposing end mills with a different helix on adjacent flutes.
Alternating the helix increased the pitch variations along the axial depth of cut hence both
the chatter free performance and the speed range were improved. Shi and Tobias [10]
considered the effects of two non linear phenomena and proposed a theory of finite
amplitude machine tool instability. The analysis is continued by Minis et al. [11] by
applying the theory of periodic differential equations on the milling dynamic equations.
This method was applied to a theoretical milling system to predict the critical depth of cut
for chatter free milling under various rotational speeds.
The chatter phenomenon actually can be suppressed by some of methods. Nakagawa et al
[12] showed that end mill with different helix angles could prevent generative chatter
vibration at lower cutting speeds and was also effective in suppressing chatter vibration at
higher cutting speed. On the other hand, a laser Doppler vibrometer has recently been
developed to observe such high frequency vibration phenomena. Furthermore, a fuzzy
logic approach for chatter suppression in end milling process is discussed by M. Liang, T.
Yeap and A. Hermansyah et al. [13]. Chatter is detected using the peak sound spectrum
amplitudes at chatter frequency ranges. In this study, the presence of permanent magnet is
investigated in suppressing the chatter phenomenon in end milling operation.
Actions (login required)
 |
View Item |