Amin, A. K. M. Nurul and Ali Asharariff, Mohd Amar and -, Syadatul Akma
(2011)
Application of permanent electromagnet for chatter control in end milling of medium carbon steel.
In:
Advanced Machining Towards Improved Machinability of Difficult-to-Cut Materials.
IIUM Press, Kuala Lumpur, Malaysia, pp. 91-97.
ISBN 9789674181758
![[img]](http://irep.iium.edu.my/style/images/fileicons/application_pdf.png) 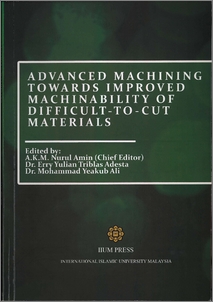 Preview |
|
PDF ( Application of permanent electromagnet for chatter control in end milling of medium carbon steel)
- Published Version
Download (554kB)
| Preview
|
Abstract
In machining process, the machine, cutting and the work piece are integrated to form structural
systems which create a dynamic characteristic. Soliman, Ismail [1] observed that vibration can
be divided into three types, free vibrations, force vibrations and self-excited vibrations (chatter).
As in this project, the focus is more on the chatter that contribute for the tool wear during the
machining of material under certain conditions of cutting processes. Chatter is an abnormal tool
behavior which it is one of the most critical problems in machining process and must be avoided
to improve the dimensional accuracy and surface quality of the product. Chatter is originated
from the disturbance that occur in the cutting zone to lack of homogeneity between surface of the
work piece, change in the types chips being produced or change in the frictional conditions at the
tool-chip interface influenced by cutting fluids being used. The forces then strain the structure
elastically and can cause a relative displacement between tool and work piece. The theory of
chatter quoted by Budak, E, and Altintas Y. [2,3] suggested the chatter as a coupling
vibration phenomenon between the workpiece and tool. Wiercigrocch M. and Budak [4]
states that mode of coupling resulted from the vibration in the thrust force direction
generate vibration in the thrust and cutting force direction. However, Amin and Anayet [5]
found that the root cause of chatter lies in the coincidence of the frequency of instability of chip
formation with one of the natural frequencies of the machine-spindle-tool system components
during end milling machining operation.
Kim et al. [6] explained that most of the drawbacks that come from chatter are excessive
tool wear, noise, tool breakage, and deterioration of the surface quality. Moreover chatter
also results in reduced material removal rate (MRR), increased costs in terms of time,
materials and energy, as well as the environmental impact of dumping non-valid final
parts and having to repeat the manufacturing process as quoted from Quintana et al. [7]. The chatter phenomenon actually can be suppressed by some of methods. Nakagawa et al
[8] showed that end mill with different helix angles could prevent generative chatter
vibration at lower cutting speeds and was also effective in suppressing chatter vibration at
higher cutting speed. On the other hand, a laser Doppler vibrometer has recently been
developed to observe such high frequency vibration phenomena. Furthermore, a fuzzy
logic approach for chatter suppression in end milling process is discussed by M. Liang, T.
Yeap and A. Hermansyah [9]. Chatter is detected using the peak sound spectrum
amplitudes at chatter frequency ranges. For this research, the study is mainly focused to
investigate the chatter amplitude effect on surface roughness at various cutting conditions with
during end milling operation of medium carbon steel.
Actions (login required)
 |
View Item |